
Case Study: Reach Robotic Manipulators
We’ve been using Reach Robotics underwater electric manipulators to carry out a range of tasks since the beginning of 2021.
In early 2022, an Offshore Wind client asked us to install some telemetry equipment from CRP Subsea in reasonably deep-water using divers. We mobilised the DSV Curtis Marshall with our Two-basket Divers Launch and Recovery System (LARS) and installed these monitoring devices to the subsea power cables. This equipment was secured with bolts fastened and torqued to 60Nm.
Later that year, we were required to re-deploy to recover this equipment and the stored data within.


ROV undoing Bolts



ROV undoing Bolts
Having two Reach Bravo manipulators, we realised it may be possible to carry out the removal operation with our Falcon ROV. The client agreed and provided a budget for conducting workshop-based trials. If successful, it would mean the works could be done diverless, with a small team off one of the client’s Crew Transfer Vessels at a significant cost saving. It would also pioneer and prove a new level of capability from an inspection-class ROV.
There were several engineering challenges. First, we would need to modify the manipulator jaws to be able to grip the large sensor housing. Secondly, we would need to mount a hex drive to the end of a manipulator. Thirdly, we would need to work out a way to increase the torque in the manipulator’s constant rotating wrist to crack bolts tightened to 60Nm. Finally, we would need to balance the ROV with additional buoyancy, to account for the extra equipment and heavy sensor so it could still fly and navigate in a tidal environment.
Our in-house fabricator got to work!
As can be seen in the above images, the main modification was a mount that clamped to the manipulator’s forearm and held a torque multiplier. This was operated by the wrist joint of the Reach Bravo. We traded speed for an increase in torque to 100Nm. The tool worked brilliantly!
​
When ready for wet-testing, we moved to the pool at our local secondary school. This allowed us to demonstrate the system to some of the students who were keen to help with the trials and learn about the subsea robotics industry.
​
After a few lessons learnt in the pool we did some further checks of the system including testing the Reach Bravo’s lift capacity. We were delighted to find that the manipulator could not only hold 10+kg at full extent, but that it could lift much heavier weights by automatically limiting its reach (we used 20kg).
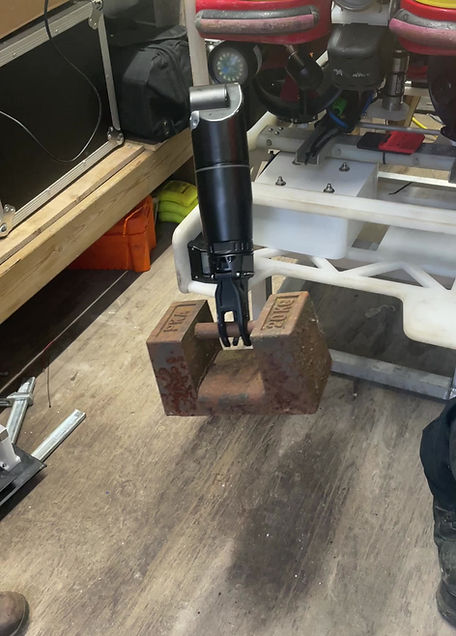
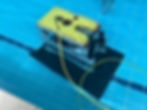

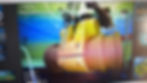
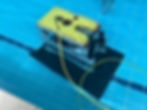
Confident in the tooling configuration, we confirmed a date and mobilised to our client’s vessel. The outcome was that we successfully unbolted and recovered both sensors within one shift, significantly quicker than we had hoped!
​
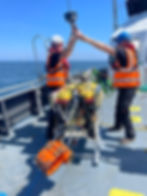
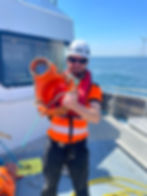
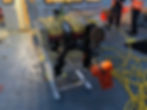
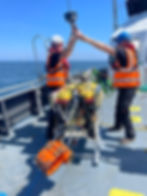
Case Study: Cleaning &
Taking CP Readings
Following our success with the sensor removal, we realised there was a lot more we could achieve with Reach Robotics technology.
Another client asked if we could investigate alternative methods to take Cathodic Protection readings from calcite-covered riser pipes in 30m of water - a task we normally undertake annually with divers. CP readings let us know if the steel is corroding or if it is suitably protected. The pipelines have an impressed current cathodic protection system which causes a hard calcite shell to form over the steel. A diver is normally required to remove the calcite exterior with a chipping hammer before taking the readings with a contact probe. But wielding a hammer is a difficult task for any ROV!
Aiming for a compact ROV solution, we purchased a Reach Bravo-3 with Stainless Steel ‘Mega’ jaws that looked like the perfect tool to grasp the riser pipes to clamp the ROV in a stable work position in order to clean a localised area of the steel. We also selected several tools to trial removing the hard calcite: an electric rotary brush, a pneumatic needle gun and some serrated teeth for bolting to the jaws of the 1kN grip-force, Bravo-3 manipulator.
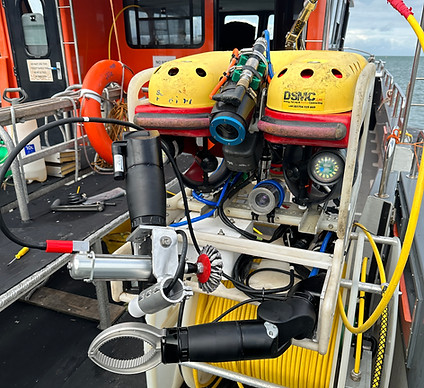
We fabricated a mounting bracket that connected to the Bravo-5’s Payload Interface accessory. Plan 'A' was for the Bravo-3 to grip the riser pipe, stabilising the ROV in the tide, while the Bravo-5 cleaned the calcite off a localised area and captured CP readings without requiring tool changes.
​
The results; rather than removing the calcite, the rotary wire-brush polished it to a smooth finish. We would like to try this brush again with a different discs. Next, we trialled the pneumatic needle gun but it couldn’t achieve the required air pressure to operate properly with the trigger held open. Finally, the serrated teeth on the ‘Mega’ jaws combined with the Bravo’s high grip force worked fantastically to crack and scratch the calcite shell off to expose clean steel.
​
Having established a successful cleaning method, we removed the calcite and took readings from all eight risers in one tidal window. We are extremely impressed by the result, especially with this class of ROV being enabled to provide such a solution. The Reach Bravo manipulator has fundamentally changed the capability of our Falcon.

With our Reach Robotics tooling increasing, we purchased the Bravo Hub to allow us to easily power, add and remove items with minimal reconfiguration time. Plus our Falcon is limited to one ethernet port on the multiplexer and very little space in the VJB to accommodate additional devices. The Bravo Hub contains a subsea switch allowing us to run multiple ethernet devices on the machine simultaneously via the single ethernet port.
We also own a Hydro-300 photogrammetry system for underwater 3D modelling requiring gigabit speed, and a 24V ‘Orphie’ low-visibility IP camera. The team at Reach made some custom modifications to our Bravo Hub, increasing the speed of the switch to Gigabit and giving us both 24V and 48V outputs; this sort of collaboration has certainly set Reach Robotics apart as a supplier.
With the Bravo Hub and tooling skid we now run our Blueview sonar, Orphie camera, Hydro-300 Photogrammetry camera, the Bravo-3, Bravo-5 and its accompanying IP wrist camera simultaneously at up to gigabit speed.
​
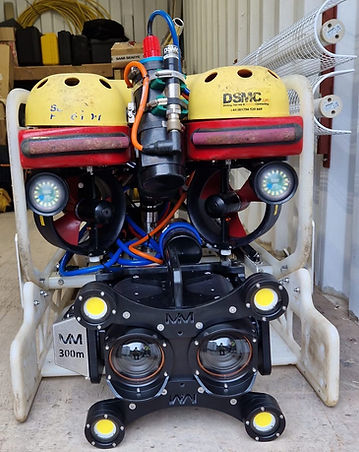